En toda empresa, como resultado del trabajo diario, los órganos de las máquinas se desgastan, la fiabilidad de los dispositivos de seguridad puede verse alterada, los trabajadores pueden ejecutar actuaciones inseguras que llegarían a convertirse en hábitos si no se controlan debidamente. Aspectos que pueden desencadenar accidentes, la mayoría de ellos graves o muy graves y que podemos evitar con seguimiento estricto del plan de mantenimiento acorde a cada instalación o equipo en particular, con una planificación de inspecciones de seguridad y todo ello de acuerdo con unos procedimientos e instrucciones de trabajo a seguir por parte de los empleados. Por otra parte aspectos como el diseño de éstas y su integración en el entorno de trabajo, si no se siguen criterios ergonómicos, puede derivar a medio plazo en trastornos musculoesqueléticos o enfermedades profesionales
A lo largo de este artículo vamos a analizar la tipología de riesgos relacionados con el uso de máquinas así como las obligaciones preventivas del empresario titular del centro de trabajo
Riesgos laborales uso de máquinas
La forma de llevar a cabo una correcta Prevención de Riesgos Laborales dentro de una empresa, se basa en una correcta evaluación de los riesgos que puedan existir. De esta forma, conociendo los posibles riesgos laborales existentes, se podrán definir las medidas preventivas dirigidas a disminuir o evitar los posibles riesgos existentes en cada uno de los puestos de trabajo. De forma general podemos encontrar 7 tipos de riesgos laborales
Los riesgos laborales más frecuentes derivados del uso de máquinas y equipos de trabajo, se pueden clasificar (entrando más en el detalle) en:
- Riesgo Mecánico
Es aquél que puede producir lesiones debidas principalmente a los elementos móviles de la máquina, o de las piezas o material con el que se trabaje. A su vez, estos se pueden subdividir en:
- Corte o seccionamiento
- Cizallamiento
- Aplastamiento
- Enganche
- Atrapamiento o arrastre
- Punzonamiento
- Fricción o abrasión
- Proyección de fluido a alta presión
2. Riesgo eléctrico
Puede producir lesiones o la muerte debido al choque eléctrico. También pueden producirse quemaduras internas y/o externas. Origen:
- Contacto eléctrico directo, con conductores activos
- Contacto eléctrico indirecto, con elementos puestos en tensión
- Fenómenos electrostáticos
- Fenómenos térmicos relacionados con cortocircuitos o sobrecargas
3. Riesgo térmico
Pueden originarse quemaduras por contacto con materiales o piezas a temperaturas extremadamente frías o muy calientes.
4. Riesgo de exposición a ruido
La exposición continua a ruido puede ocasionar en unos casos pérdida permanente de audición, y en otros, fatiga, estrés y trastornos generales.
5. Riesgo de exposición a vibraciones
Pueden ocasionar trastornos musculares (mano, lumbago, ciática,…), además de trastornos de tipo neurológico y vascular.
6. Riesgo de exposición a las radiaciones
Éstas pueden ser:
- Ionizantes, procedentes de fuentes radiactivas como: equipos de radiografía, eliminadores de cargas estáticas radiactivas. (infrecuentes en la enseñanza)
- No ionizantes, que las podemos encontrar en hornos de microondas, en procesos de calentamiento por inducción y dieléctrico, en operaciones de soldadura al arco eléctrico, en técnicas de impresión por ultravioleta,… (fáciles de encontrar en centros de formación profesional) .
7. Riesgo de exposición a sustancias peligrosas
Éstas pueden desprenderse en el procesado de los materiales, ocasionando riesgo higiénico para los operarios que pudieran inhalarlos o entrar en contacto con ellos.
8. Riesgos ergonómicos
El operador puede sufrir trastornos físicos por la adopción de posturas incorrectas o la necesidad de realizar esfuerzos mayores que los que serían propios de la tarea.
9. Riesgo de incendio
10. Riesgo de explosión
Mantenimiento preventivo de máquinas e instalaciones.
Obligaciones preventivas del empresario
En cumplimiento del artículo 16.1 de la Ley 31/1995, de Prevención de Riesgos Laborales (LPRL), el empresario deberá integrar la prevención de riesgos laborales en el sistema general de gestión de la empresa y, por lo tanto, deberá contar con la implicación y colaboración de diferentes actores en la consecución de este fin. Corresponderá dicha obligación al empresario titular de las instalaciones quien deberá de asegurarse:
- Las instalaciones son adecuadas a las características del lugar de trabajo en el que van a prestar servicio
- Las instalaciones se utilizan dentro de los límites de funcionamiento previstos por el fabricante y siguiendo las instrucciones de estos o de los instaladores, con el adecuado adiestramiento previo a los trabajadores
- las instalaciones se mantienen conforme a un plan de mantenimiento, bien siguiendo lo establecido en la reglamentación industrial específica aplicable, bien atendiendo a criterios basados en la experiencia del usuario y en las instrucciones de los fabricantes e instaladores cuando no exista dicha reglamentación; el plan de mantenimiento recogerá las instalaciones afectadas, las operaciones a realizar, la periodicidad, los responsables y el registro final
- Las instalaciones se someten a inspecciones iniciales tras su ejecución y antes de la puesta en servicio y/o a controles periódicos, siguiendo los criterios establecidos por la reglamentación de seguridad industrial vigente;
- Las instalaciones se someten a revisiones adicionales cuando se han producido hechos excepcionales como transformaciones, accidentes, fenómenos naturales o falta prolongada de uso, que puedan tener consecuencias perjudiciales para la seguridad y salud
- Las revisiones de mantenimiento y las inspecciones son efectuadas por personal competente, para lo cual designará a las personas responsables de contactar con la empresa ins-taladora o mantenedora o, en su caso, con un Organismo de Control (OC), de atenderles durante la visita, de guardar los registros emitidos, etc.
- Los trabajadores que vayan a realizar las tareas de mantenimiento, reparación o transformación poseen la formación y el adiestramiento necesarios cuando estas operaciones supongan un riesgo específico para su seguridad y salud;
- Los trabajadores que utilicen las instalaciones, así como sus representantes, reciben una formación e información adecuadas sobre los riesgos derivados de la utilización de las mismas, así como sobre las medidas de prevención y protección que deban adoptarse
- Se conservan, durante toda su vida útil, los resultados de las inspecciones y revisiones de las instalaciones, que deben estar documentadas y a disposición de la autoridad laboral;
- Se anulan o retiran aquellas instalaciones o equipos que dejan de cumplir los requisitos de seguridad necesarios
Obligaciones del empresario. Marco reglamentario
El marco reglamentario que regula con carácter general las condiciones de seguridad y salud en el trabajo, fija la necesidad de que los lugares de trabajo y los distintos equipos y máquinas en ellos instalados y utilizados dispongan de un mantenimiento que garantice la conservación de las prestaciones de seguridad de los mismos a lo largo de su vida útil.
- El Real Decreto 485/1997 sobre Disposiciones de Seguridad y Salud en el Trabajo en su anexo I, punto 4 establece que «los medios y dispositivos de señalización deberán ser, según los casos, limpiados, mantenidos, y verificados regularmente, y reparados o sustituidos cuando sea necesario, de forma que conserven en todo momento sus cualidades intrínsecas y de funcionamiento».
- El Real Decreto 486/1997, de 14 de abril, por el que se establecen las disposiciones mínimas de seguridad y salud en los lugares de trabajo en su Anexo II apartado 4 dice «los lugares de trabajo y, en particular, sus instalaciones, deberán ser objeto de un mantenimiento periódico, de forma que sus condiciones de funcionamiento satisfagan siempre las especificaciones del proyecto, subsanándose con rapidez las deficiencias que puedan afectar a la seguridad y salud de los trabajadores. Si se utiliza una instalación de ventilación, deberá mantenerse en buen estado de funcionamiento y un sistema de control deberá indicar toda avería siempre que sea necesario para la salud de los trabajadores. En el caso de las instalaciones de protección, el mantenimiento deberá incluir el control de su funcionamiento».
- El Real Decreto 773/1997 de 30 de mayo, sobre disposiciones mínimas de seguridad y salud relativas a la utilización por los trabajadores de equipos de protección individual en su artículo 7.1 establece que «la utilización, el almacenamiento, el mantenimiento, la limpieza, la desinfección cuando proceda, y la reparación de los equipos de protección individual deberá efectuarse de acuerdo con las instrucciones de los fabricantes».
- El Real Decreto 1215/1997, de 18 de julio, por el que se establecen las disposiciones mínimas de seguridad y salud para la utilización de los trabajadores de los equipos de trabajo en su artículo 3 apartado 5 establece que «el empresario adoptará las medidas necesarias para que, mediante un mantenimiento adecuado, los equipos de trabajo se conserven durante todo el tiempo de utilización en unas condiciones tales que garanticen totalmente la seguridad y salud de los trabajadores durante la utilización de tales equipos de trabajo. Dicho mantenimiento se realizará teniendo en cuenta las instrucciones del fabricante, las características de los equipos, sus condiciones de utilización y cualquier otra circunstancia normal o excepcional que pueda influir en su deterioro o desajuste. Las operaciones de mantenimiento, reparación o transformación de los equipos de trabajo cuya realización suponga un riesgo específico para los trabajadores sólo podrán ser encomendadas al personal especialmente capacitado para ello». Así mismo, en el punto 14 del Anexo II del citado RD se establece que «las operaciones de mantenimiento, ajuste, desbloqueo, revisión o reparación de los equipos de trabajo que puedan suponer un peligro para la seguridad de los trabajadores se realizarán tras haber parado o desconectado el equipo, haber comprobado la inexistencia de energías residuales peligrosas y haber tomado las medidas necesarias para evitar su puesta en marcha o conexión accidental mientras esté efectuándose la operación. Cuando la parada o desconexión no sea posible se adoptarán las medidas necesarias para que estas operaciones se realicen de forma segura o fuera de las zonas peligrosas». En el punto 15 del Anexo II se establece que «cuando un equipo de trabajo deba disponer de un diario de mantenimiento, éste permanecerá actualizado».
Un análisis más detallado, en función del sector o agente de riesgo:
- El Real Decreto 1389/1997, de 5 de septiembre, por el que se aprueban las disposiciones mínimas destinadas a proteger la seguridad y la salud de los trabajadores en las actividades mineras en el punto 3 de la parte A de su Anexo obliga a establecer «un plan adecuado que deberá prever la inspección sistemática, el mantenimiento y, en su caso, la comprobación de los equipos e instalaciones mecánicos y eléctricos. El mantenimiento, la inspección y la comprobación de cualquiera de las partes de las instalaciones o equipos deberá realizarse por personal competente. Deberán elaborarse y archivarse adecuadamente fichas de inspección y comprobación». Además «deberá mantenerse siempre listo para su utilización un material de seguridad adecuado y en buen estado de funcionamiento. El mantenimiento deberá realizarse teniendo en cuenta las actividades que se ejerzan».
- El Real Decreto 1627/1997, de 24 de octubre, por el que se establecen disposiciones mínimas de seguridad y de salud en las obras de construcción en su artículo 10 d) establece que durante la ejecución de la obra se aplicará «el mantenimiento, el control previo a la puesta en servicio y el control periódico de las instalaciones y dispositivos necesarios para la ejecución de la obra, con objeto de corregir los defectos que pudieran afectar a la seguridad y salud de los trabajadores».
- El Real Decreto 374/2001, de 6 de abril, sobre la protección de la salud y seguridad de los trabajadores contra los riesgos relacionados con los agentes químicos durante el trabajo en su artículo 4 c) dice que los riesgos para la salud y la seguridad de los trabajadores en trabajos en los que haya actividad con agentes químicos, se eliminarán o reducirán al mínimo mediante «el establecimiento de los procedimientos adecuados para el uso y mantenimiento de los equipos utilizados para trabajar con agentes químicos peligrosos, así como para la realización de cualquier actividad con agentes químicos peligrosos, o con residuos que los contengan, incluidas la manipulación, el almacenamiento y el traslado de los mismos en el lugar de trabajo».
- El Real Decreto 614/2001, de 8 de junio, sobre disposiciones mínimas para la protección de la salud y seguridad de los trabajadores frente al riesgo eléctrico en su art. 3.3 establece que «las instalaciones eléctricas de los lugares de trabajo se utilizarán y mantendrán en la forma adecuada y el funcionamiento de los sistemas de protección se controlará periódicamente, de acuerdo a las instrucciones de sus fabricantes e instaladores, si existen, y a la propia experiencia del explotador».Asimismo, en el art. 3.4 añade que «en cualquier caso, las instalaciones eléctricas de los lugares de trabajo y su uso y mantenimiento deberán cumplir lo establecido en la reglamentación electrotécnica, la normativa general de seguridad y salud sobre lugares de trabajo, equipos de trabajo y señalización en el trabajo, así como cualquier otra normativa específica que les sea de aplicación».
Guía para la gestión preventiva de las instalaciones de los lugares de trabajo
En el año 2019 el INSST publicó la Guía para la gestión preventiva de las instalaciones de los lugares de trabajo. Selecciona 11 tipos de instalaciones. Para cada una de ellas, el documento resume y simplifica sus distintas fases por las que pasan desde que se diseñan hasta que se ponen fuera de uso o se desmantelan, según los requisitos establecidos en la normativa de seguridad industrial. Además en la guía se indican los diferentes aspectos que un técnico de prevención puede controlar para asegurar que se cumplen los aspectos normativos más relevantes relacionados con la puesta en funcionamiento, la conservación y el buen uso de la instalación y, por lo tanto, con la seguridad de los trabajadores afectados por la presencia de las mismas en los lugares de trabajo.
- Almacenamiento de productos químicos
- Centros de Transformación eléctrica
- Instalaciones de gases combustibles
- Instalaciones de protección contra incendios
- Líneas aéreas de alta tensión
- Instalaciones petrolíferas
- Instalaciones frigoríficas
- Instalaciones eléctricas de baja tensión
- Instalaciones térmicas
- Instalaciones de ascensores
- Instalaciones de equipos a presión
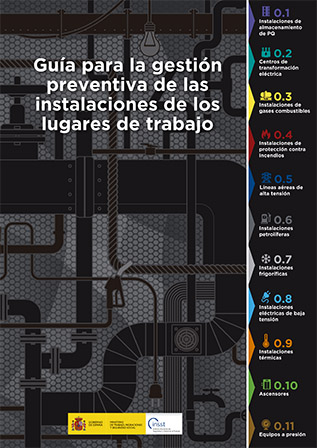
La gestión preventiva de los equipos de trabajo. Fases
Como hemos visto el empresario, en cumplimiento de su deber de proteger la seguridad y salud de sus trabajadores, deberá extender la actividad preventiva a todas las instalaciones existentes para así garantizar un adecuado control de los riesgos asociados a las mismas.
El apartado 4º del anexo II del Real Decreto 486/1997 establece la obligación del empresario (en este caso, el titular de las instalaciones) de llevar a cabo un mantenimiento periódico de las instalaciones presentes en su centro de trabajo. La normativa específica o, en su defecto, el manual de instrucciones o la información del instalador, indicará cómo, quién y cuándo deberá actuar en este sentido. En caso contrario, será el empresario titular de la instalación quien deberá determinar cómo llevar a cabo estas actuaciones, apoyándose, cuando sea necesario, en la evaluación de riesgos existente.
Con objeto de examinar periódicamente las condiciones peligrosas que presenten o puedan presentar equipos e instalaciones, por diseño, funcionamiento o situación dentro del contexto del área de trabajo ese ha de establecer un programa de revisiones de seguridad y mantenimiento de los equipos de trabajo. El programa irá acompañado de procedimientos de trabajo para cada una de las actuaciones preventivas a realizar, herramientas indispensables para prevenir los riesgos implícitos a su uso y mantenimiento. Si tenemos en cuenta que el mantenimiento de equipos se realiza por empresas subcontratadas, especialistas en la realización de estas operaciones correctivas o preventivas definidas, será de vital importancia a la hora de realizar la coordinación de actividades empresariales que cada uno de nuestros equipos tenga detallado los riesgos de su uso y mantenimiento, instrucciones de trabajo y procedimientos preventivos relativos.
La gestión preventiva de los equipos de trabajo se realizará en 3 fases diferenciadas:
- Planificación de revisiones de seguridad y mantenimiento
Se elaborará un plan de mantenimiento que incluya las revisiones periódicas o preventivas y las comprobaciones o inspecciones necesarias, teniendo en cuenta las instrucciones del fabricante y del instalador; en caso de no existir dichas instrucciones, se tendrán en cuenta las características de las instalaciones, las condiciones de utilización y cualquier otra circunstancia que pueda influir en su deterioro o desajuste. Se deberá tener en cuenta el marco legal e información del manual de instrucciones de máquinas y equipos de trabajo
Dos Tipos de revisiones
- Las inspecciones reglamentarias de seguridad industrial , que derivan de requisitos legales y deben de llevarse a cabo por empresas acreditadas o entidades autorizadas de inspección y control. Tal es el caso de aparatos a presión, ascensores, vehículos, etc., para los que es obligatorio el certificado de inspección de organismos de control autorizados.
- Las observaciones preventivas del trabajo sirven para verificar el correcto cumplimiento de las normas de trabajo establecidas, de los procedimientos de trabajo implantados y del uso de los EPI entregados y, por tanto, para detectar desviaciones en las actuaciones previstas, con el fin de incorporar las mejoras que se estimen oportunas. Las suelen realizar personas con mando, con el objeto de establecer un diálogo del que surjan las mejoras necesarias en la forma de realizar las tareas, especialmente si éstas son peligrosas o incómodas.
2. Plan de mantenimiento e inspecciones de seguridad
Estas revisiones e inspecciones pueden venir impuestas, como hemos visto, por una normativa industrial de aplicación o procedimiento interno de mantenimiento. En el primer caso serán realizadas principalmente por organismos de control o por los órganos competentes de cada comunidad autónoma, pudiendo ser también realizadas, según la instalación de que se trate, por el propio empresario, por un técnico competente o por una empresa instaladora mantenedora acreditada.
Cuando no exista normativa industrial aplicable, el titular de la instalación deberá asegurarse de que las revisiones e inspecciones periódicas están contempladas en el plan de mantenimiento
3.Registro de los resultados de los controles periódicos de las instalaciones y análisis